마크포지드 활용사례 : 지멘스 에너지 어플리케이션 센터
- J&Tek Corp.
- 2023년 10월 25일
- 3분 분량
Siemens Energy Technology Application Center
THE CUSTOMER

Siemens Energy Technology Applications Center(TAC)는 산업 래피드 솔루션의 개념부터 완성을 지원하는 세계 최고 수준의 기관입니다. 로봇 공학, 스캐닝, 디지털 툴, 적층 제조 및 절삭 가공을 비롯한 다양한 기술을 사용하여 산업 문제에 대한 설계, 엔지니어링 및 신속한 프로토타이핑 솔루션을 제공합니다.
TAC는 Siemens Energy의 글로벌 엔지니어링 비즈니스를 지원하며 다양한 고객의 설계 및 엔지니어링 문제를 해결합니다. TAC의 기술 포트폴리오에 가장 최근에 추가된 Markforged의 시뮬레이션은 엔지니어가 Eiger™ 작업 내에서 부품의 강도와 강성을 가상으로 테스트할 수 있도록 지원합니다. 이를 통해 엔지니어는 프린팅에 적용되는 연속 섬유 소재의 활용과 배치를 최적화하여 부품 강도와 프린팅 시간 및 비용 간의 균형을 맞출 수 있습니다.

제작사례 1 : Gas Turbine Vane Fixture
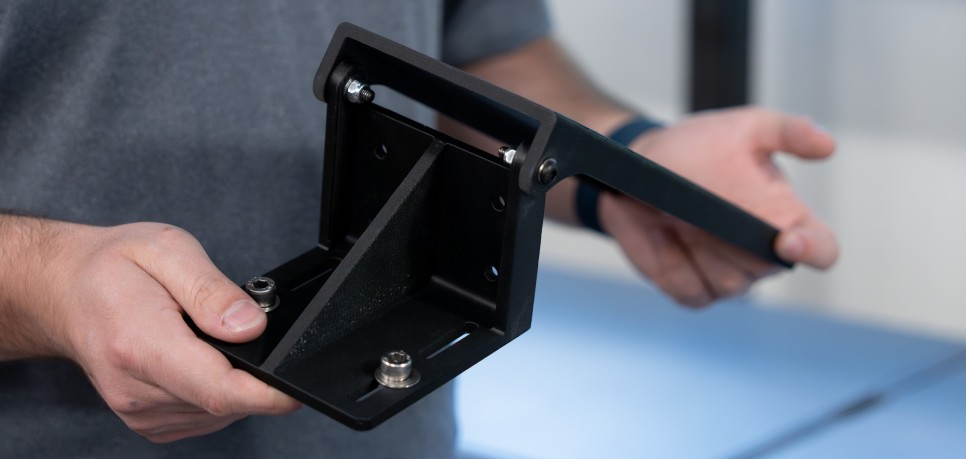
Showcased above is the Gas Turbine Vane Fixture
THE CHALLENGE
Siemens Energy는 전 세계 고객에게 전기를 공급하는데 사용되는 대형 가스 터빈 엔진을 생산합니다. 이 엔진에는 엔진의 연료가 점화된 후 뜨거운 가스의 흐름을 제어하는 여러 개의 정적 베인 링이 포함되어 있습니다. 해 인코넬 베인은 최대 4,000°F의 온도에서도 보호되는 세라믹 코팅이 되어 있습니다. Siemens Energy는 Digital Forge를 사용하여 부품을 지속적으로 테스트하고 가스 터빈의 효율 개선에 중요한 설계 아이디어를 반복적으로 검증합니다.
TAC에서 새로운 설계 아이디어를 테스트할 때 사용되는 기술 중 하나는 온열 열화상 기술입니다. 이 기술은 뜨거운 공기가 베인의 내부 냉각 채널을 통과하는 동안 적외선 카메라가 부품 표면의 열 발생 결과를 이미지화하는 기술입니다. 엔지니어는 세라믹 코팅이 과도하게 마모되거나 성능이 저하된 부분과 응력 신장의 징후가 있는지를 찾습니다.
평균 무게가 15파운드, 길이가 최대 3피트인 베인은 엔진 작동 모의 실험에서 최대 600°F 온도의 공기가 통과하는 동안 고정 장치에 단단히 고정되어 있어야 합니다. 고정 장치에서 베인이 떨어지면 수천 달러의 손상이 발생할 수 있습니다. 뿐만 아니라 손상이 단순한 엔진 마모로 인한 것인지, 아니면 베인이 바닥에 떨어져서 발생한 것인지 파악하기도 어렵습니다.
이전에는 이러한 테스트 중에 베인을 고정하기 위해 금속 및 가스켓 고정 장치를 사용했습니다. 그러나 이러한 고정구는 가공하는데 최대 6주가 걸렸고 실리콘 가스켓은 성형하는 데 최대 $10,000의 비용이 들었습니다. 때문에 TAC 팀은 베인을 단단히 고정할 수 있을 만큼 고정 장치의 강도를 높이기 위해 연속 탄소 섬유 비율이 높은 Onyx를 사용하여 고정 장치를 제작하기 시작했습니다.
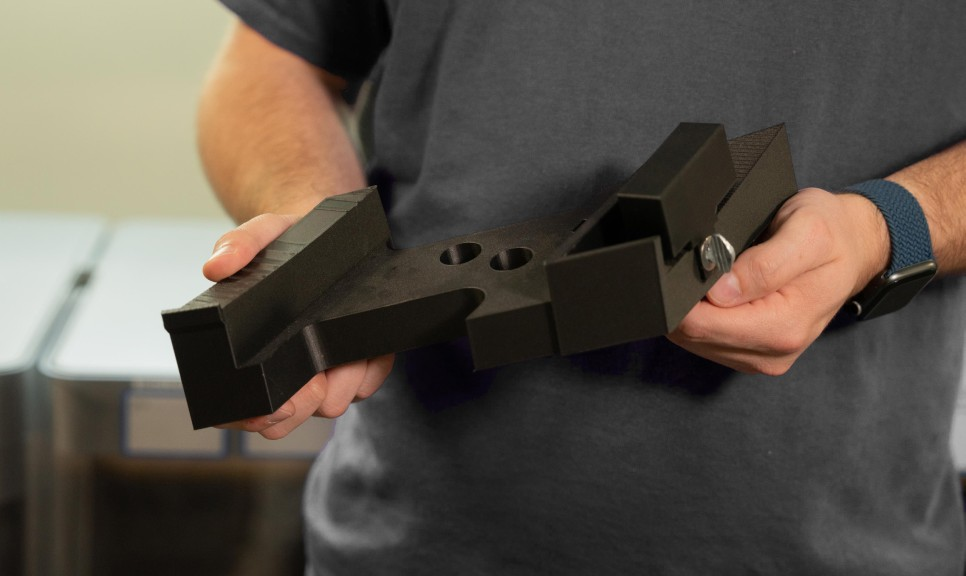
Showcased above is the Gas Turbine Vane Fixture
THE SOLUTION TAC 팀은 새로운 시뮬레이션이 통합된 Eiger™ 새로운 버전을 베타 테스트할 기회가 있었습니다. 이때 그들은 이를 강도와 프린트 시간에 맞게 맞춤형 구조물을 최적화할 수 있는 기회로 삼고, Markforged의 시뮬레이션을 통해 시간과 비용을 보다 효율적인 방식으로 이용하여 내구성이 뛰어난 구조물을 제작할 수 있게 되었습니다. 시뮬레이션 결과, 부품 설계자는 연속 섬유 보강(CFR)이 부품의 강도 또는 강성에 미치는 영향에 대한 확신이 없었기 때문에 필요한 강도를 달성하는 데 필요한 것보다 더 많은 탄소 섬유를 사용하는 경우가 많다는 사실을 알게 되었습니다. 시뮬레이션을 통해 CFR이 설계에 미치는 영향에 대한 확신을 얻음으로써 이러한 문제를 극복할 수 있었습니다. 이를 통해 탄소 섬유 사용량을 60%까지 줄이고 프린트 시간을 최대 75%까지 단축할 수 있었습니다. 또한 TAC 팀은 시뮬레이션을 통해 엔지니어가 기존의 유한 요소 해석(FEA)을 통해 구조물 설계를 실행하는 데 필요한 시간보다 훨씬 짧은 시간 내에 설계 최적화를 수행할 수 있다는 사실을 발견했습니다. Markforged의 시뮬레이션은 경계 조건 적용을 통해 사용자를 안내하는 것과 부품에 사용된 Markforged 소재에 최적화되어 있습니다. 또한 TAC 팀은 Eiger™ 작업 내에서 이 구조 분석을 효율적으로 수행할 수 있습니다.

Simulation software in Eiger shown above
Manufacturing Time and Cost Comparison

제작사례 2 : Robot Arm Backpack

Showcased above is the Robot Arm Backpack
THE CHALLENGE
일부 정밀 검사 어플리케이션의 경우 로봇 팔을 사용하여 센서를 테스트 대상 부품에 가깝게 배치합니다. Backpack은 로봇의 '전완부' 위에 놓이는 트레이입니다. 여기에는 프로그래밍 가능한 로직 컨트롤러, 센서, 공기 시스템 및 팔 끝 센서를 지원하는 기타 구성 요소가 포함되어 있습니다. TAC는 다양한 센서를 수용하기 위해 다양한 Backpack 구성을 생성합니다. 어플리케이션 개발 과정에서 로봇 엔드 이펙터에 있는 센서의 수와 유형이 달라질 수 있으며, 이로 인해 Backpack 구성이 변경될 수 있습니다.
기존의 금속으로 제작된 Backpack은 제작에 상당한 시간이 걸리기 때문에 프로젝트 도중 Backpack 디자인을 업데이트할 수 있는 빈도가 제한됩니다. 대형 Backpack에 3D프린팅을 사용할 때의 단점은 일반적으로 기존 금속 Backpack보다 유연하고 원치 않는 관성이 로봇 팔에 전달 된다는 점입니다.

THE SOLUTION
로봇 팔 Backpack을 Onyx로 제작하면 TAC 팀은 Backpack의 디자인을 빠르게 반복할 수 있습니다. 예를 들어, 새로운 버전이 나올 때마다 새로운 장착 지점과 기타 필요한 기능을 쉽게 추가할 수 있습니다. Markforged의 시뮬레이션을 사용하면 최적의 구조적 특성을 신속하게 달성하여 제작 시간과 더 견고한 구조의 필요성 사이의 균형을 맞출 수 있습니다. 시뮬레이션을 통해 TAC 팀은 프린트 전에 설계의 약점을 확인할 수 있었습니다.

Simulation software in Eiger shown above.
Manufacturing Time and Cost Comparison

THE FUTURE
TAC 팀이 Markforged의 시뮬레이션을 채택한 이유는 몇 가지 주요 이점을 제공하기 때문입니다. 첫째, 부품 설계에 대한 빠르고 정확한 구조 분석을 제공하여 빠른 프린트 시간에 대한 요구와 구조적으로 견고한 부품에 대한 요구 사이의 균형을 맞출 수 있습니다. 또한 이 데이터는 고객과 논의할 때 3D 프린팅으로 생산된 부품의 구조적 기능에 대한 근거를 제시하는 데 도움이 됩니다.
또한 TAC 팀은 Markforged의 시뮬레이션이 파트 강도뿐만 아니라 프린트 시간에도 영향을 미치는 각 파트에 대한 최적의 프린트 방향을 결정할 때에도 도움이 된다는 사실을 발견했습니다.
해당 소프트웨어가 발전함에 따라 TAC 팀은 이 소프트웨어가 융합 필라멘트 제조(FFF) 3D 프린팅 부품 개발에 필수적인 도구가 될 것이라고 확신합니다.
Comments